你知道組裝一部手機(jī)需要多少個部件嗎?你知道生產(chǎn)一部手機(jī)需要用多長時間嗎?
你可能很難想像,原來組裝一部手機(jī),需要涉及多達(dá)1000個物料,100多道工序。
你是否能在腦海里描繪出這樣一幅畫面:整個生產(chǎn)基地,從大卡車向基地運貨、物料自動倉儲入庫、生產(chǎn)線自動提取配件、成品出庫,全線采取智能化管理。生產(chǎn)組裝環(huán)節(jié)采用人機(jī)結(jié)合,機(jī)器完成大部分工作。整個生產(chǎn)制造流程,從一個零件的傳輸,到最后成品的運送,主要工作基本都是由機(jī)器人獨立操作完成。
2015年,華為每條產(chǎn)線員工上百人,生產(chǎn)一部手機(jī)需要10分鐘,而現(xiàn)在,只需17名工人,每28.5秒產(chǎn)出一臺手機(jī)。
這個了不起的數(shù)字背后是國產(chǎn)制造技術(shù)的飛躍進(jìn)步,中國速度的真實寫照,更說明了生產(chǎn)自動化和智能化設(shè)備為制造產(chǎn)業(yè)帶來的生產(chǎn)周期、質(zhì)量和效率的同步改善,這是精細(xì)化成本管理和科技發(fā)展的成果。
據(jù)悉,2020年國內(nèi)市場5G手機(jī)累計出貨量1.63億部,25年全球手機(jī)出貨量有望達(dá)到15億臺(IDC預(yù)測,CAGR3.6%)。在如此大的市場體量下,這必然要求手機(jī)的生產(chǎn)、組裝、檢測等環(huán)節(jié)都有很高的自動化和智能化水平。?
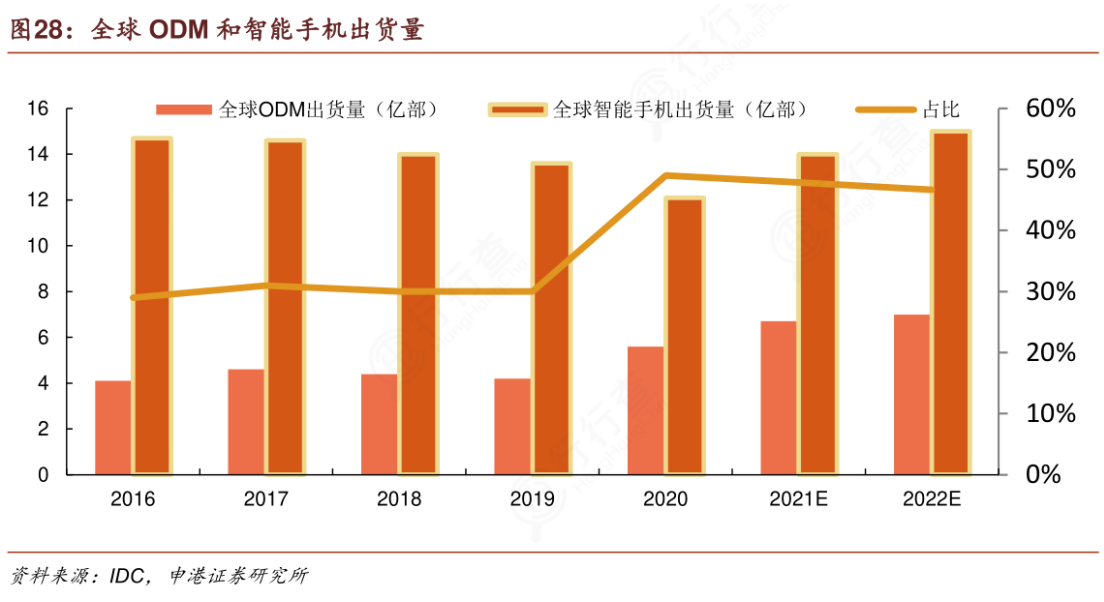
圖片來源于行行查
為了確保手機(jī)組裝的成品具備高可靠性,品質(zhì)檢測決定了每臺手機(jī)的出廠身份證是否為“綠碼”。
而手機(jī)缺陷檢測,不僅有手機(jī)內(nèi)部沖壓件尺寸的精密測量、手機(jī)邊框的點膠檢測,還有手機(jī)外殼的污點劃痕、手機(jī)外包裝的字符識別等等,需要檢測的缺陷種類繁多且復(fù)雜多變。使用檢查、引導(dǎo)和識別性能的技術(shù)和裝備來檢測,就會讓復(fù)雜的事情變得簡單起來。
今天我們?yōu)榇蠹伊信e3個手機(jī)檢測案例,來呈現(xiàn)3D視覺檢測在手機(jī)檢測中的優(yōu)勢:
?
客戶檢測需求:
檢測膠寬、膠高及斷膠。
檢測方法:
1、用3D輪廓儀掃描,對整體產(chǎn)品成像,以點膠接觸底面建立基準(zhǔn)面;
2、整個長膠路分成兩個檢測區(qū)域,使用軌跡檢測工具進(jìn)行膠路膠寬、膠高、斷膠缺陷檢測。
檢測結(jié)果:
精確檢測膠路寬度和高度信息判別點膠質(zhì)量。
檢測需求:
檢測產(chǎn)品邊緣高度。
檢測方法:
1、用3D輪廓儀掃描,對整體產(chǎn)品成像;
2、選取產(chǎn)品中間任意N個區(qū)域為基準(zhǔn),擬合平面,計算邊緣與平面之間的高度差。
檢測結(jié)果:
重復(fù)性精度在0.01-0.02mm左右。
客戶檢測需求:
檢測多種類型螺釘浮高。
檢測方法:
1、用3D輪廓儀掃描,對產(chǎn)品整體成像,以產(chǎn)品邊沿特征建立坐標(biāo)系作定位;
2、用4個區(qū)域檢測工具提取螺釘頂端區(qū)域,在螺釘周圍用基準(zhǔn)平面工具選取3個區(qū)域擬合基準(zhǔn)面;
3、輸出螺釘頂端到基準(zhǔn)平面的段差 。
檢測結(jié)果:
螺釘高度檢測靜態(tài)重復(fù)性為5um左右。
手機(jī)殼高度差3D檢測示意
以上是昂視在手機(jī)制造業(yè)視覺解決方案中的小部分實例,在以往的項目中,昂視LP系列3D輪廓儀的不俗表現(xiàn)均獲得客戶廣泛認(rèn)可。
基于在機(jī)器視覺領(lǐng)域逾八年的豐富經(jīng)驗和雄厚研發(fā)功底,針對手機(jī)制造業(yè)不斷更新的需求,昂視能為手機(jī)制造企業(yè)提供2D視覺、3D視覺及讀碼檢測需求的整體解決方案,確保在手機(jī)生產(chǎn)環(huán)節(jié)應(yīng)對如檢測、對位、測量、OCR 以及一維和二維條碼讀取等種類繁多的檢測,滿足客戶各種應(yīng)用的精確要求。?